The use of an ultrasound bench is the most common method for detecting mainly delamination defects within the composite material. The operator uses this measuring device to drive ultrasonic waves, which will perform a "sound path" inside the carbon tubes that we use to make some connecting rods. It is the echo of this wave, represented by a curve on a monitor, that will be interpreted by the controller to determine if the defect is (or not) acceptable, with respect to a determined threshold.
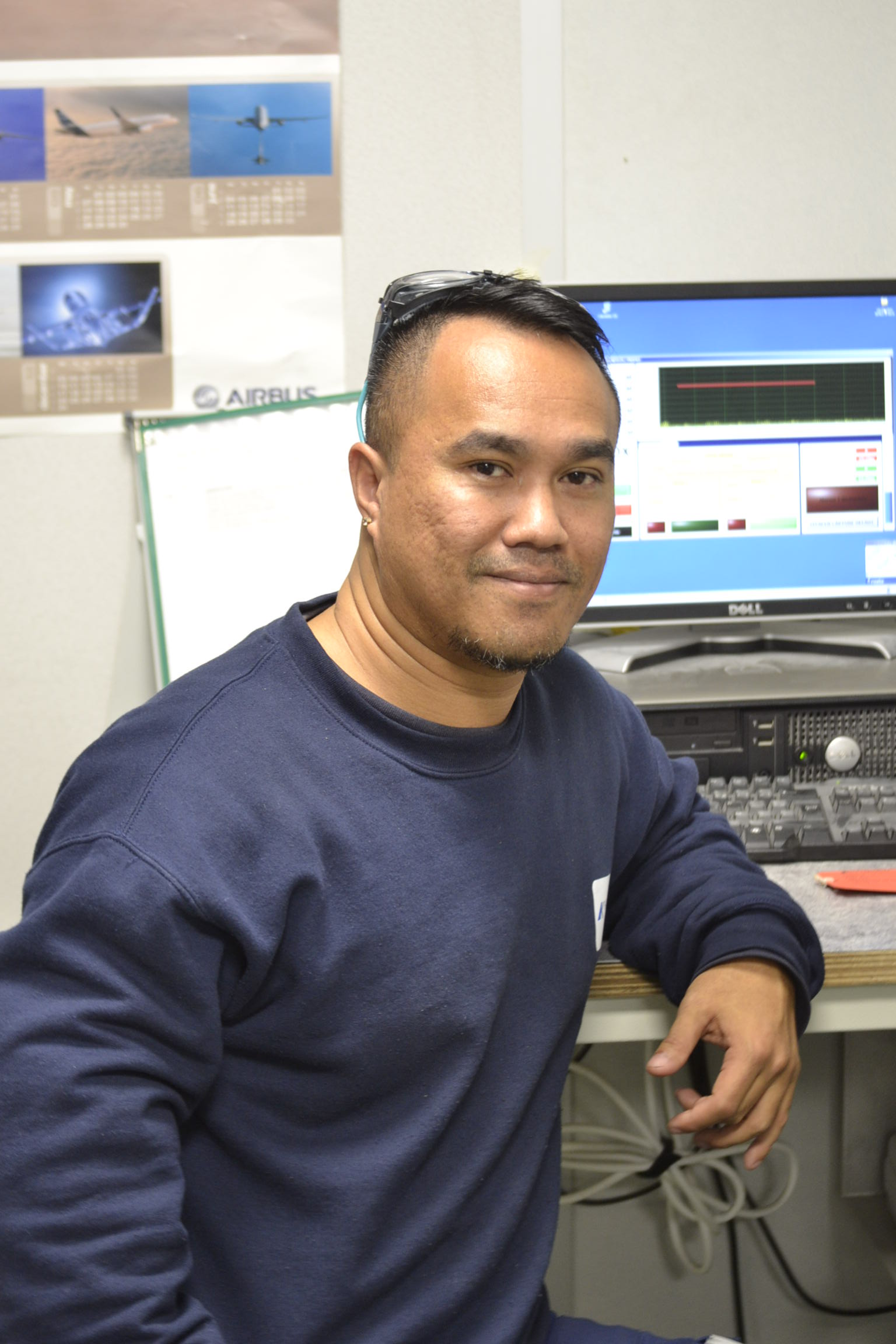
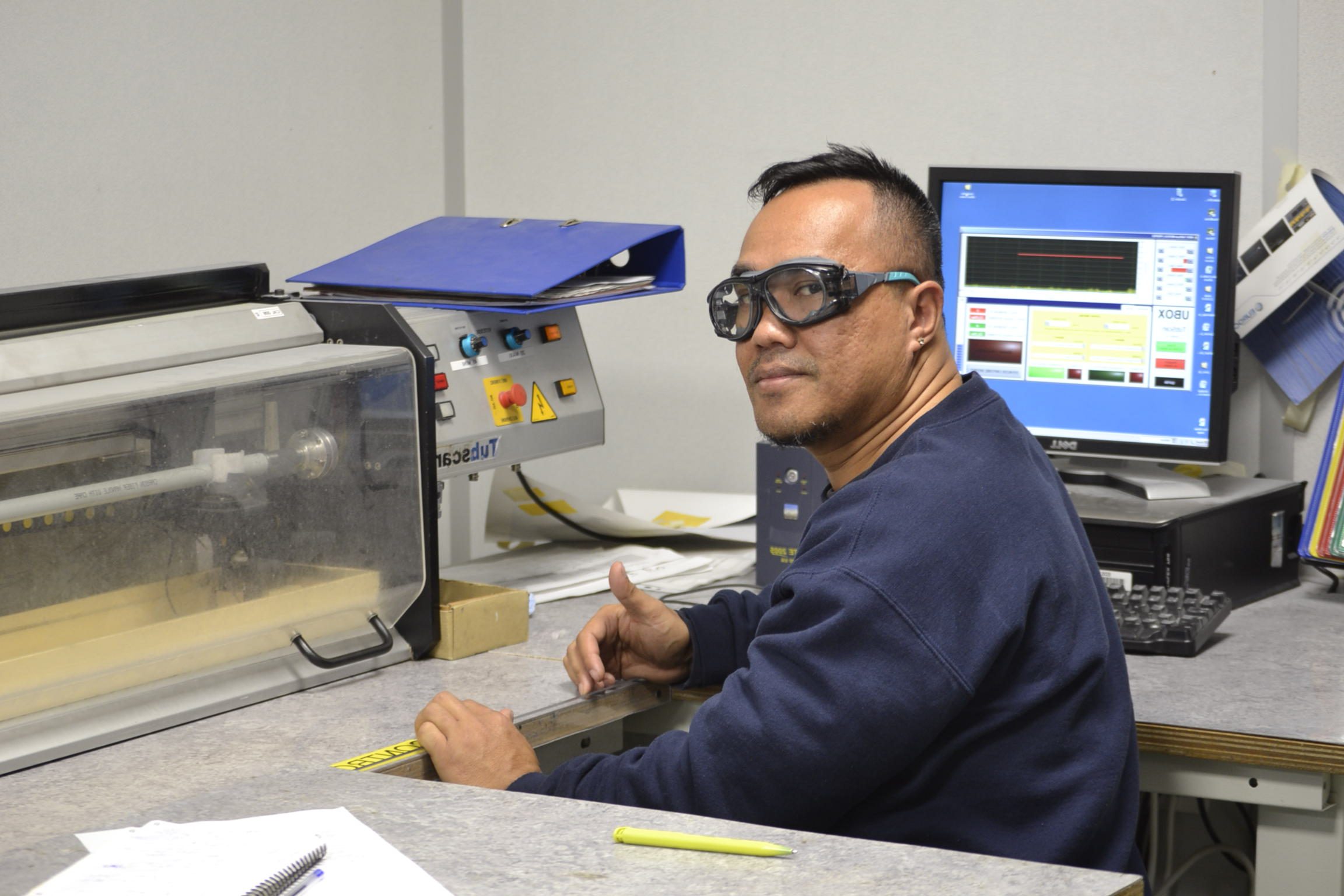
To understand the principle of ultrasonic control, you need to see it as an echo that returns sound at the top of a cliff. The sound wave takes a while to go through the material (air in this example, composite material in our profession), and when it reaches an obstacle (the cliff, or a material defect) the wave is sent back to the emission point. Depending on how long the sound wave takes to return, and since we know how fast it will travel in the material, the computer calculates how far the defect is from the end of the part (starting area of the impulse), and by cross-checking with amplitude tests, we can even manage to accurately determine the size of the defect, it is all this work of investigation and expertise that makes this profession so interesting. I would never have imagined that all my math and physics classes would be such a big part of my daily working life!